Metal Replacement
Castello cambio automotive riprogettato in ottica additive
Nel settore Automotive, come in tutti i settori industriali, riuscire a ridurre il peso e i tempi di produzione di un componente diventa sempre più strategico. Se a questi due obiettivi aggiungiamo anche la necessità di eliminare i costi di attrezzatura per serie limitate e piccole produzioni, ecco che l’ Additive Manufacturing diventa una soluzione efficace e vantaggiosa.
La tecnologia però da sola non basta, per raggiungere vantaggi concreti è necessario anche riprogettare i componenti per renderli adatti ad una produzione Additiva.
Obiettivi del progetto
- Semplificazione del processo produttivo
- Alto livello di personalizzazione (eliminazione dei tools)
- Riduzione dei tempi di produzione
- Riduzione peso
- Aumento prestazionale
- Riduzione dei costi di produzione
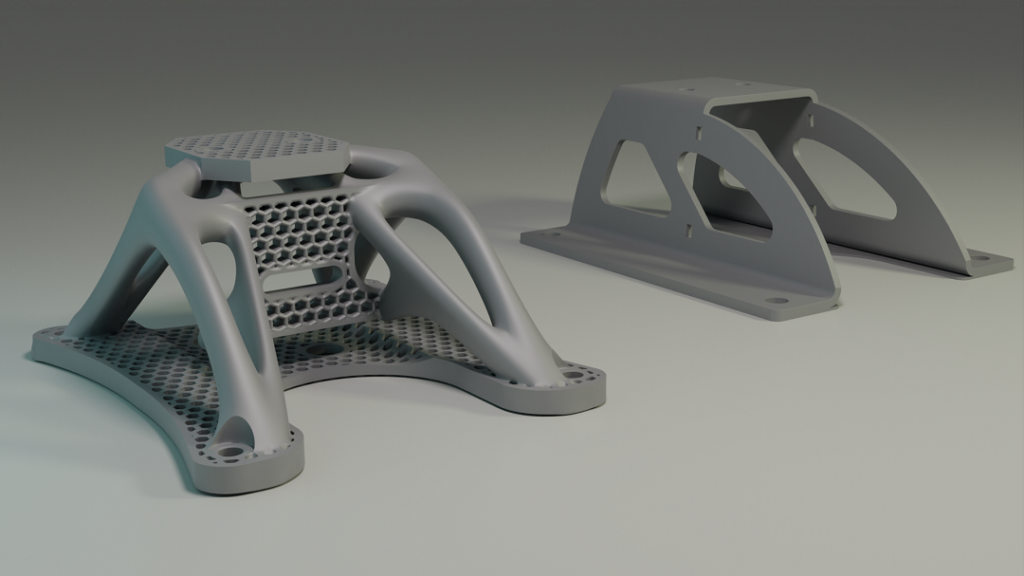
pROBLEMA
Realizzare un componente da taglio laser, piegatura di lamiera e successivo assemblaggio quando si tratta di tirature limitate può diventare problematico sia a livelli di costi che di tempistiche di produzione.
SOLUZIONE
Utilizzare il concetto di metal replacement creando una geometria nuova che soddisfi i requisiti di progetto e che permetta di ridurre i costi della materia prima (polimero invece che metallo), e ridurre i pesi e allo stesso tempo avere forme che semplificano il processo di stampa 3D.
SVILUPPO
Partendo dal componete originale, avendo definito i carichi e i vincoli tramite una serie di iterazioni abbiamo progettato un componente unico da stampare in PA12.
Abbiamo quindi sostituito il metallo con la plastica senza inficiare le prestazioni del componente.
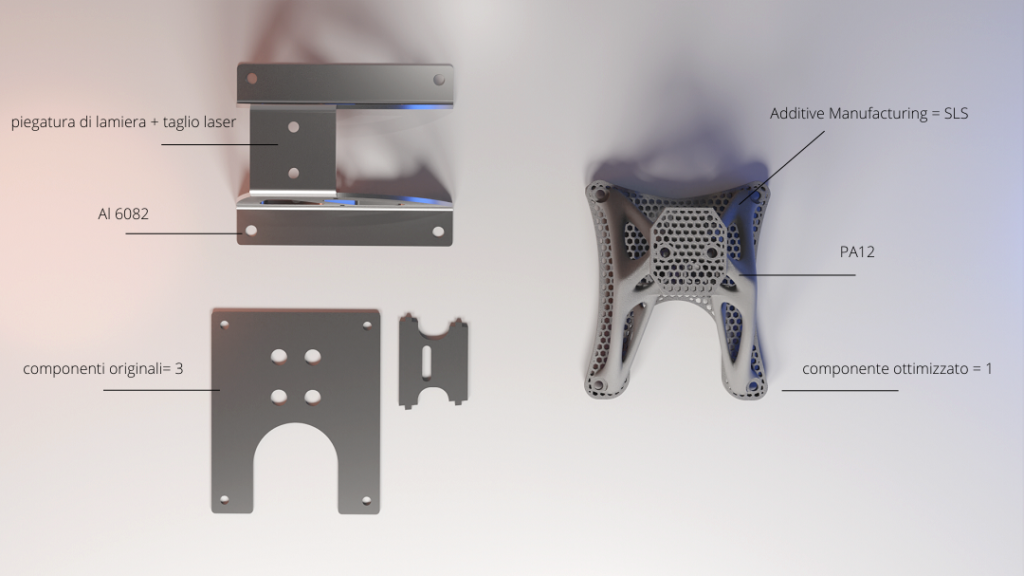
Intro
Nel mondo della produzione esistono esigenze che mettono in crisi le tecnologie tradizionali. Ad esempio creare componenti ad hoc o con complessità geometriche (talvolta nemmeno troppo complesse) può stressare l’utilizzo di una tecnologia come lo stampaggio ad iniezione, CNC o la piegatura di lamiera.
Come esempio portiamo il castello del cambio delle auto, componente che spostandoci in ambiente racing, esaspera le sue richieste sia per prestazioni meccaniche che per leggerezza.
Questo è uno dei settori in cui la produzione customizzata o costantemente variegata è un’esigenza e non un’esotica visione di business futuristica, rivoluzionaria ed ecosostenibile. Tutto ciò ci porta a sottolineare meglio i vantaggi e di conseguenza le risoluzioni che la stampa 3D (additive manufacturing) ci offre a livello di DNA tecnologico.
Ma è veramente una tecnologia valida per questa tipologia di problematiche? Funziona? Basta la tecnologia da sola?
Beh noi siamo di parte lavoriamo in questo mondo, quindi la nostra risposta è…NO!
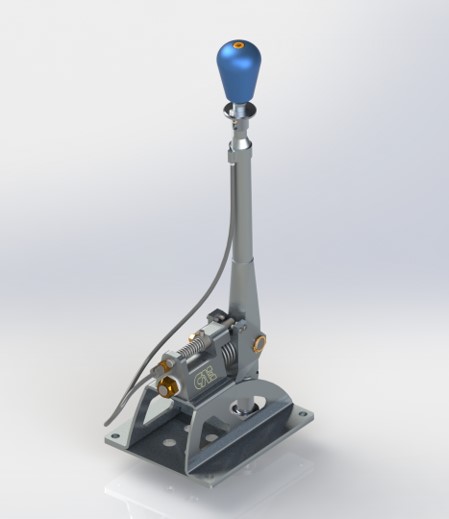
Immagine da progetto grabcad “cae-shifter-for-bmw
Il progetto
La stampa 3D è una delle tecnologie di produzione (non più solo di prototipazione!!!) e come tale bisogna assisterla, metterla nelle giuste condizioni per farla rendere al meglio. Hai mai visto una F1 alla Dakar? Quindi la verità che per questa tematica nello specifico la tecnologia si sposa molto bene non avendo necessità di stampi o tools vari, essendo rapida nell’esecuzione ed avendo a disposizione differenti materiali per sostituire quello utilizzato precedentemente.
Per le cose semplici e dove non si cerca il risparmio (di materiale, peso, tempo e soprattutto costo!) questo potrebbe funzionare ma non basta in generale. Il pezzo mancante che per tutte le altre tecnologie viene dato per scontato e direi sottointeso ma talvolta sottovalutato, è la PROGETTAZIONE. Che vuol dire tante cose tra cui tradurre il concetto in pratica e farlo parlare nella stessa lingua della tecnologia. Inoltre questa tecnologia, rivoluzionaria e prepotente, si permette (solo quando sfruttata) di aprire a nuove possibilità, prima razionalmente e LOGICAMENTE impossibili da realizzare e quindi completamente fuori da ogni possibile valutazione. Una di queste tematiche è il METAL REPLACMENT.
Lo Sviluppo
In questo caso la creazione di un castello del cambio leggero e rigido porta ad utilizzare due strade di costruzione: 1° dal pieno CNC, 2° da lamiera. Se il primo ha dei limiti nella geometria e nel costo, il secondo richiede differenti passaggi sia per la produzione che il conseguente montaggio di tutte le parti in un solo componente.
Di conseguenza queste complicazioni portano ad avere un processo costoso e più lento rispetto all’ AM e con risultati a livello di prestazioni più bassi. Ovviamente la scelta di un materiale metallico (stiamo parlando di produzione classica) è necessaria per il risultato che si vuole ottenere ma nel mondo della stampa 3D si può ragionare in modo differente, ci sono anche altre strade.
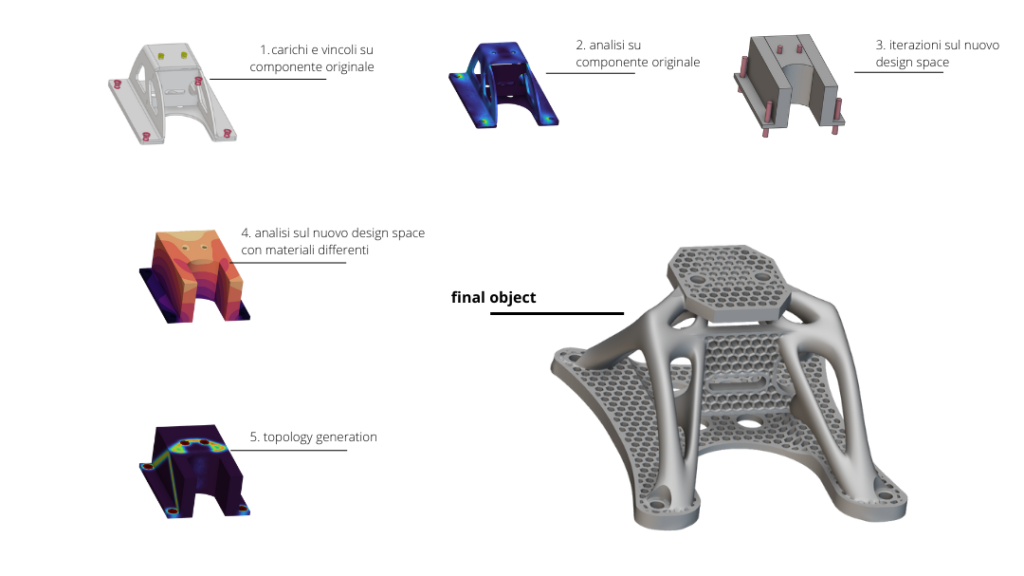
Dopo avere valutato in che modo deve lavorare il componente e a che ti tipi di sforzo sia sottoposto la strada del metal replacement ci dice di valutare le prestazioni su un polimero a confronto con il metallo. Ed è qua che ci viene in assistenza la geometria, l’unico modo per sostituire un componente metallico con un polimerico senza accorgersi di nulla.
Forma = Funzione
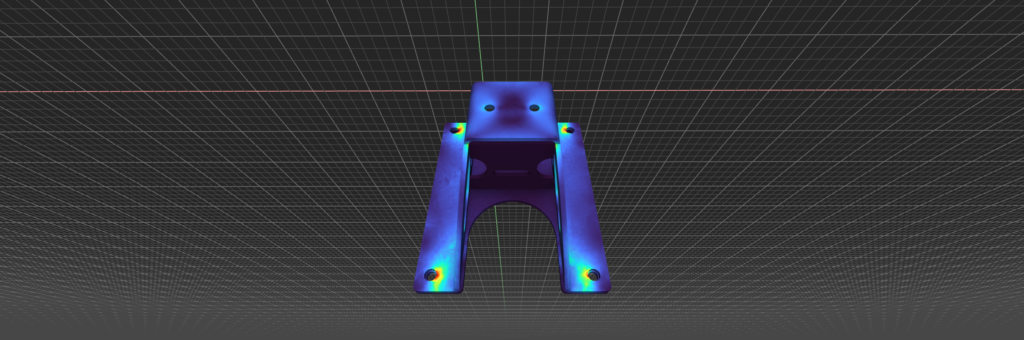
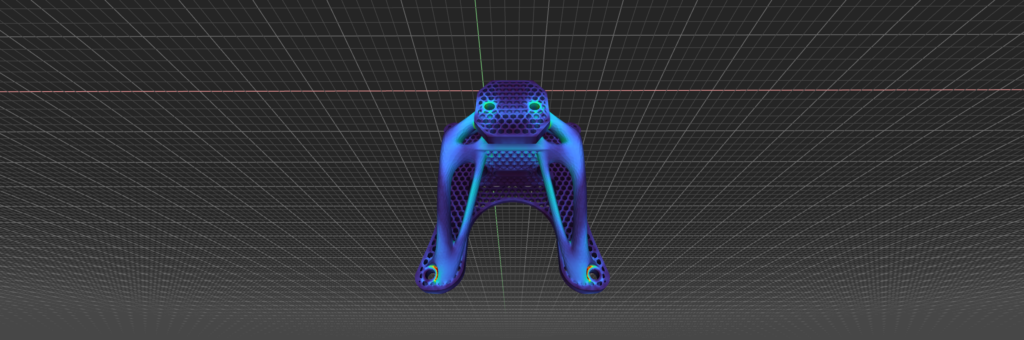
La differenza sta nel fatto che per questa tecnologia abbiamo molti meno vincoli, quindi più forme possibili, quindi più funzioni possibili.
Quello che abbiamo fatto è valutare l’ingombro e quindi delineare uno spazio, questo perché non vogliamo modificare i componenti attorno, lo lasciamo nel suo habitat natale. Quindi definito il volume fatte le analisi FEM ridisegniamo alcune versioni. Non basta solo alleggerire dove gli sforzi non sono alti, ma se vogliamo avere più vantaggi possibili è necessario lavorare anche sulle distribuzioni. Quando si ottimizza, il range tra lo stress minimo e quello massimo diventa un valore fondamentale per capire la bontà della geometria. Seguono altri loop iterativi, ora per affinare ora rifinire ma questo sempre seguendo un metodo, il quale è fondamentale per avere una ripetibilità della risoluzione del problema. Il metodo è fondamentale anche per lo sviluppo del componente in se stesso e in relazione all’assieme.
Abbiamo raggiunto questi molteplici obiettivi partendo da una problematica e sfruttando al massimo le opportunità che l’AM offre. Si tratta di un cambiamento del processo produttivo con la conseguente modifica del modello di business più sostenibile. Questa è una delle strade percorribili, siamo certi che continuando a reiterare si possono raggiungere ulteriori livelli di ottimizzazione.
Il progetto in numeri
Riduzione tempo
2/3 settimane
vs
1 settimana
Riduzione peso
- 62%
Riduzione costi
384€ cad
vs
88€ cad
Riduzione stress
- 38%