Valvola stampata in 3D
complessità degli elementi di progettazione e produzione
Le geometrie complesse disponibili con la fabbricazione additiva sono indubbiamente uno dei fattori più attraenti quando si cerca di introdurre la stampa 3D in qualsiasi flusso di lavoro produttivo, ma la realtà è che la maggior parte delle soluzioni di test non distruttivi disponibili semplicemente non può fornire test sufficientemente dettagliati per parti destinate all’uso in applicazioni critiche. Con il metodo di NDT a risonanza non lineare di Theta che diventa oggetto di discussione nella comunità della fabbricazione additiva, gli addetti al settore di 3dpbm hanno individuato l’opportunità perfetta per mettere alla prova le credenziali di RD1-TT e hanno avviato un progetto collaborativo tra Theta Technologies e gli specialisti di progettazione 3D di Puntozero.
Obiettivi del progetto
- Portare l’AM in produzione
- Effettuare test ripetibili su larga scala
- Rendere affidabile l’AM
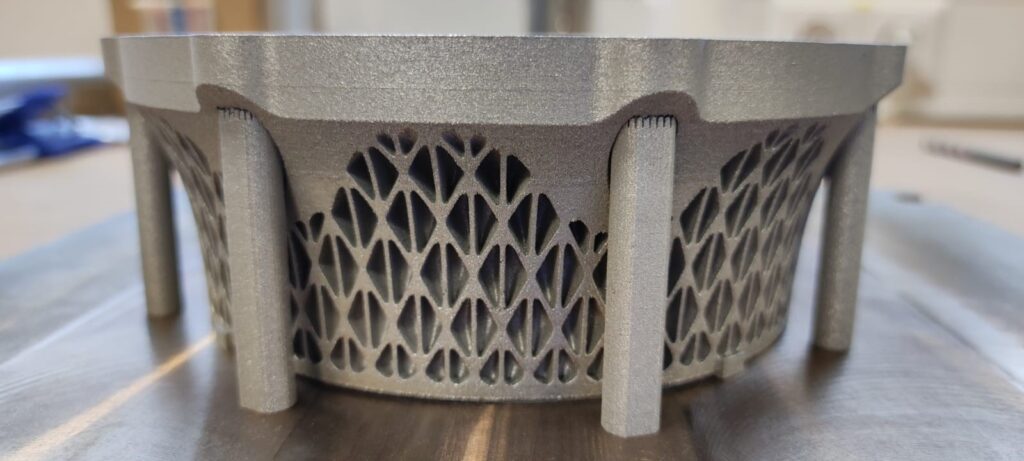
pROBLEMA
Il problema affrontato nel progetto è la limitata adozione della fabbricazione additiva di metallo per parti destinate agli utenti finali, soprattutto in applicazioni critiche, a causa delle restrizioni delle attuali soluzioni NDT (Non-Destructive Testing). Le soluzioni di testing non distruttivo disponibili non forniscono test sufficientemente dettagliati per garantire l’uso sicuro di queste parti in contesti critici.
SOLUZIONE
La soluzione proposta è RD1-TT, una nuova tecnologia NDT sviluppata da Theta. Questa tecnologia è stata progettata appositamente per superare le limitazioni esistenti e offrire ai progettisti di stampa 3D la possibilità di dimostrare appieno le capacità di queste parti complesse. RD1-TT è in grado di effettuare test più dettagliati, permettendo una valutazione più accurata delle parti fabbricate con stampa 3D in metallo, rendendole più adatte per applicazioni critiche.
SVILUPPO
Il progetto ha coinvolto una collaborazione tra Theta Technologies e Puntozero, specialisti di progettazione 3D. L’iniziativa ha incluso la messa alla prova delle credenziali di RD1-TT attraverso test e valutazioni dettagliate, con l’obiettivo di dimostrarne l’efficacia nel superare le limitazioni precedentemente riscontrate nella fabbricazione additiva di metallo per applicazioni critiche.
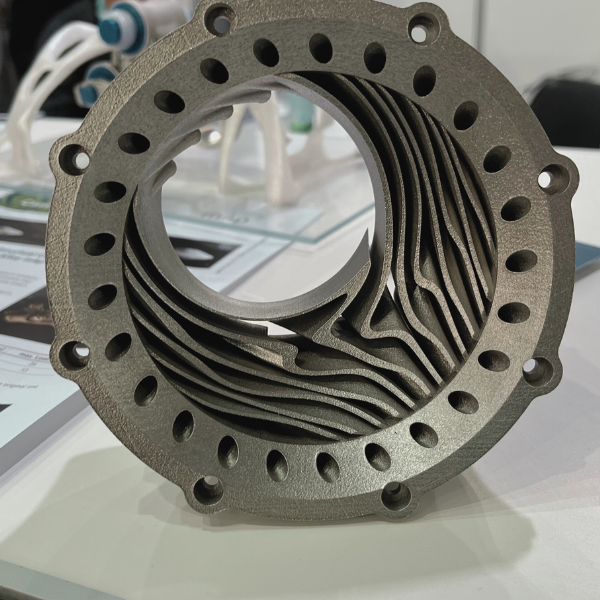
Intro
Negli ultimi anni, non è stato facile utilizzare la stampa 3D di metallo per fare parti importanti che la gente usa, soprattutto in situazioni critiche.
Questo perché le soluzioni attuali per testare queste parti non sono abbastanza buone.
Ora c’è una soluzione chiamata RD1-TT, una nuova tecnologia di test che Theta ha creato apposta.
Questa tecnologia è pensata per aiutare design e progettisti, dando loro la possibilità di dimostrare le vere capacità di ciò che creano.
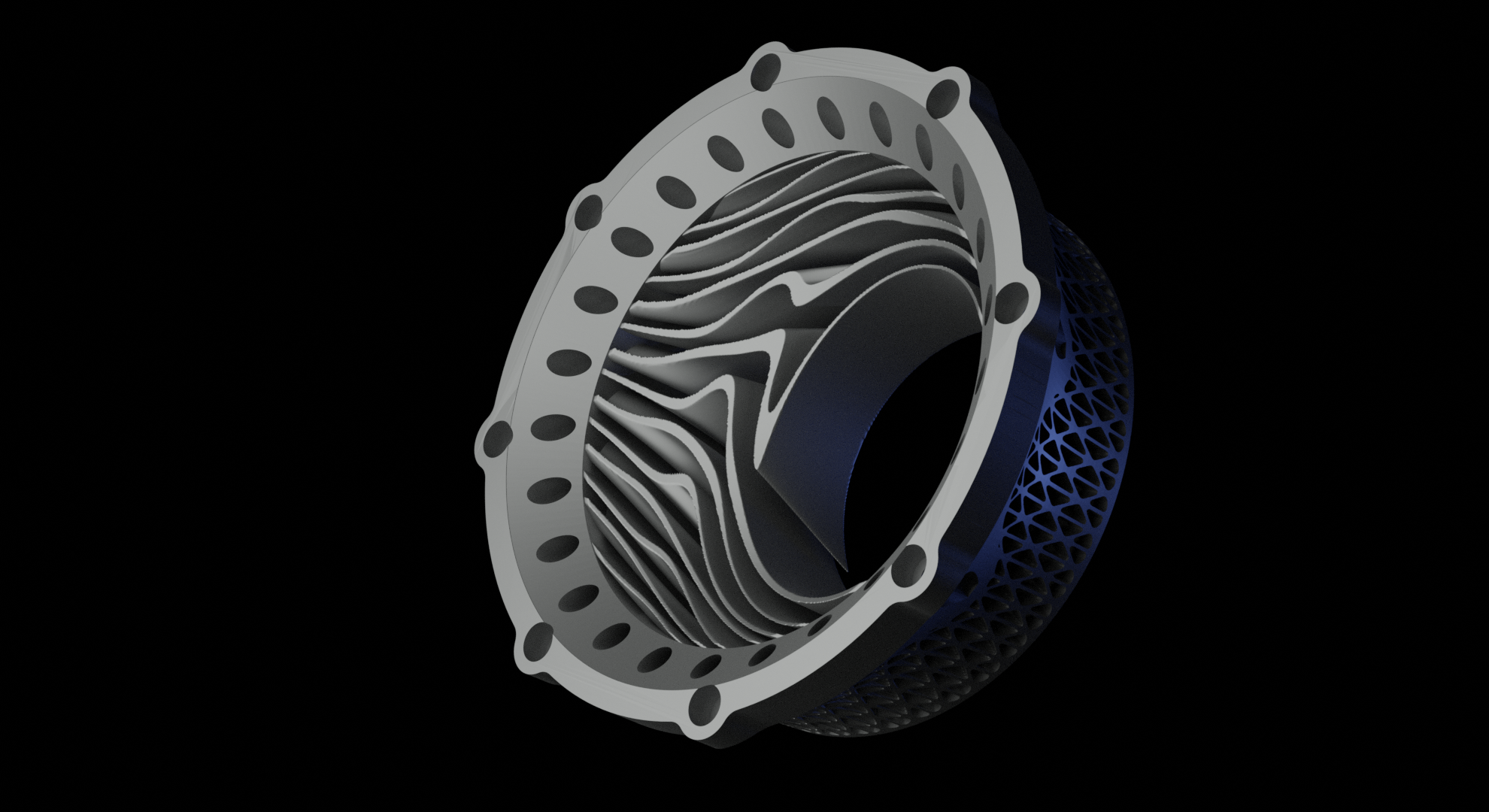
Il progetto
Puntozero ha collaborato con il produttore di polvere metallica m4p per testare la tecnologia di risonanza non lineare di Theta su valvole stampate in 3D. Le valvole, progettate da Puntozero e stampate con la tecnologia m4p, presentavano caratteristiche complesse. Il test riuscito confermerebbe l’efficacia della tecnologia di Theta nel testare componenti complessi stampati in 3D e avvalorerebbe l’attenzione dettagliata di m4p nella produzione di polvere metallica, in particolare nella scelta di materiali adatti come la lega Superduplex.
Lo Sviluppo
Le valvole, progettate da Puntozero e soggette al test non distruttivo, sono state stampate utilizzando le stampanti interne di m4p e presentano molteplici caratteristiche di design complesse, un aspetto che non influenza il test di risonanza non lineare.
La scelta del materiale appropriato per le parti stampate in 3D è un fattore chiave per il successo complessivo di un componente. Bastian Kallenbach, ingegnere di sviluppo presso m4p, comprende l’importanza di apprendere ogni dettaglio di ciascuna parte e capire il suo uso previsto per selezionare il materiale più adatto. “A causa delle specifiche esigenze per i materiali di trasporto fluidi, è stata selezionata la lega Superduplex altamente resistente alla corrosione m4p™ Type10-SDX come abilitatore adatto. Il suo profilo di caratteristiche corrisponde anche a un ragionevole livello di resistenza all’usura, oltre a una processabilità adattabile, che consente di controllare geometrie soggette a stress residui e quindi stamparle in modo affidabile e riproducibile”.
Un test di successo delle valvole stampate in 3D confermerebbe non solo le credenziali di Theta nel test non distruttivo di componenti complessi stampati in 3D, ma convaliderebbe anche l’attenzione meticolosa di m4p verso la produzione di polvere metallica.
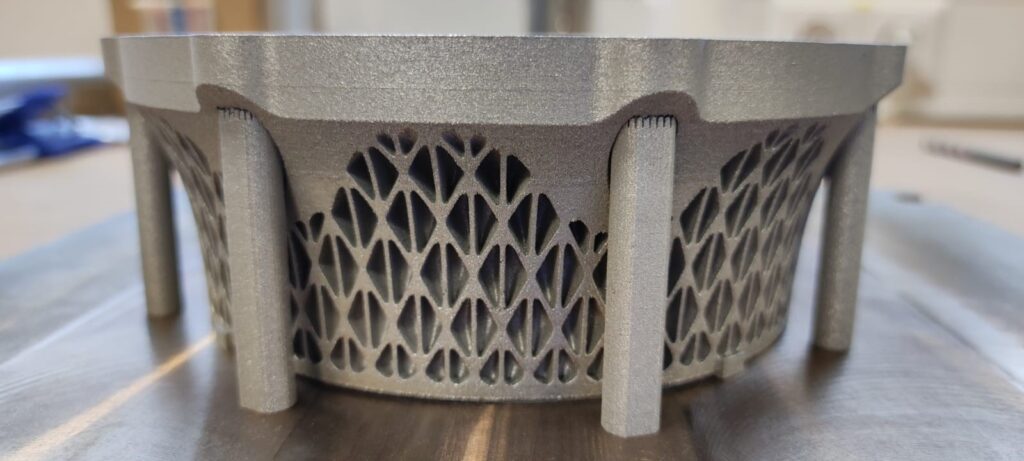
Sblocca il potenziale dell'AM
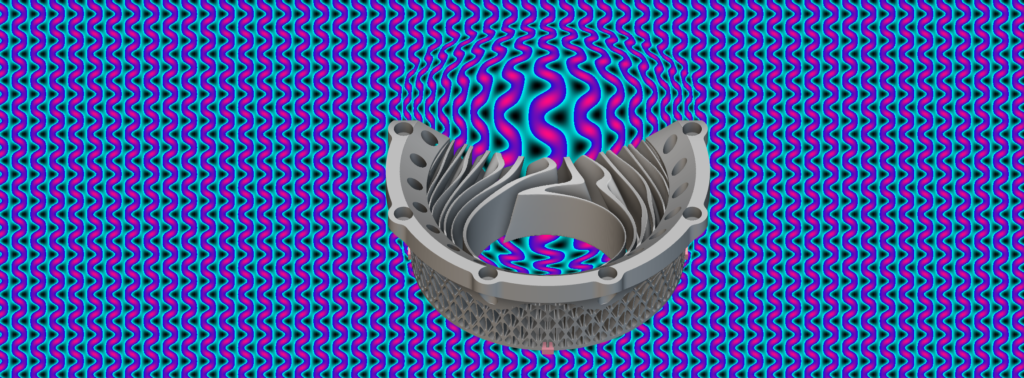
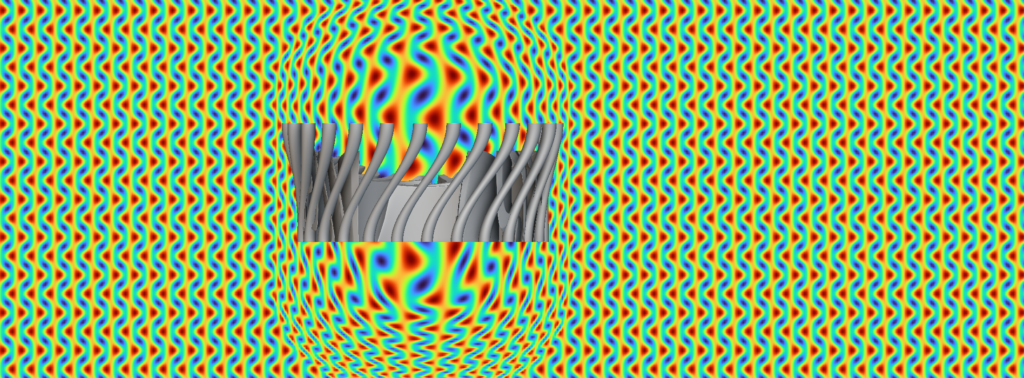
Ciò rende RD1-TT la soluzione perfetta per l’implementazione come tecnica rapida di triage o per coloro che cercano di utilizzare la fabbricazione additiva per la produzione di massa. Un test di risonanza non lineare viene eseguito eccitando un componente al fine di generare una risposta lineare.
Il processo di test complessivo convalida ciò che Theta Technologies ha sempre creduto, ovvero che le parti metalliche stampate in 3D, sempre più complesse, possono ora essere sottoposte a un processo di test non distruttivo rapido e, soprattutto, accurato. Quando utilizzato in un ambiente produttivo, RD1-TT può essere impiegato per testare componenti metallici stampati in 3D immediatamente dopo la stampa. Ciò offre ai produttori una comprensione istantanea dell’integrità di una parte, che, se difettosa, può essere rimossa dal flusso di lavoro prima di aggiungere valore inutile attraverso passaggi aggiuntivi come la lavorazione successiva.
Le limitazioni di progettazione dei metalli stampati in 3D che erano effettivamente imposte ai progettisti a causa della mancanza di metodi di test non distruttivi efficaci in grado di gestire parti complesse sembrano destinati a diventare un problema del passato.
Questa sarà una notizia gradita per i progettisti e produttori di fabbricazione additiva che cercano di spingere i limiti del design e adottare la stampa 3D di metalli come opzione reale per la produzione di massa..